A visit to Fujifilm
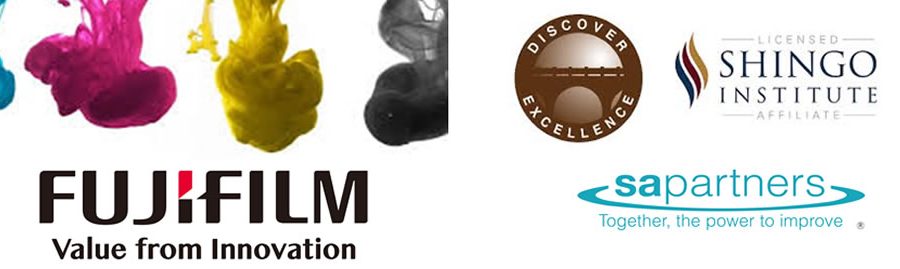
Fujifilm Speciality Ink Systems (Fujifilm) achieved the highest ranking of any manufacturing site on our visit feedback last year with an outstanding +97% NPS Score. It is no surprise to anyone that has been to the site, as it not only meets, but sets, world class standards in visual management, Five S and lean deployment.
More importantly, the visit to Fujifilm stands out because of the emphasis they place on culture, and the obvious commitment to creating an environment where continuous improvement (CI) and Lean is owned by every employee.
The site at Broadstairs employs 320 (180 in Operations) and is primarily a chemical blending operation. They manufacture speciality inks for the digital and analogue printing industries. Exporting over 6,200 tonnes of finished product to 86 countries they achieve over 97% right first-time delivery levels – an industry-leading standard.
I have been visiting this site for over 10 years, and each time the new initiatives impress me, the latest being the introduction of Kamishibai and Electronic Process Control (Takt) Boards. Excellent tools which are delivering great productivity and performance improvements.
I have highlighted some information on these and some of the other learnings from their recent visit.
A Sustainable Lean Programme
Underpinning CI at Fujfilm is a home grown Lean deployment framework. A dedicated CI team of three people supports this – Gary Burgess, Gary Page and Adam Murrell.
When developing their programme Fujifilm recognized that not all of the lean tools could or should be applied at once, so they developed ‘Building Blocks’ to highlight and manage those initiatives that would drive CI through the organization, and keep a focus on quality.
Many of these areas will be familiar to those that have studied Lean or Continuous Improvement, but what makes it work is that this has not changed in ten years. The consistency and determination to re-enforce their commitment to best practice has allowed them to achieve outstanding levels of operational excellence.
Fujifilm are very open about their journey with visitors, and shared the following lessons:
- It doesn’t matter what it’s called – Lean, WCM, CI – choose terminology that is homegrown and personal.
- Communicate – and communicate some more (see below).
- Get some early hits to gain momentum (Quick Wins)
- Don’t have a big launch & never ever use the term ‘initiative’
- Capture every problem as an opportunity to improve.
- Empower people & give them responsibility
- Manage expectations – upwards, downwards & outwards
- Remember & Celebrate success
Kamishibai Boards (Short Interval Control)
One of the most recent additions to the Fujifilm lean toolbox has been the introduction of Kamishibai boards to assist in daily, weekly and monthly task management in many areas of the business. This latest tool has been adopted with enthusiasm by Team Leaders, operators and office staff as it provides a simple, visual task reminder. The Kamishibai boards are a short interval control mechanism to ensure repetitive tasks are completed, such as Autonomous Maintenance, Consumable replenishment and audit control. (picture here)
Lean All areas – Laboratory and Beyond
Fujifilm are justifiably proud of how well lean and workplace organisation has been adopted in every area of the site. The laboratory is one of the finest examples of workplace organisation you could find in the UK and the improvements introduced have led to significant cost savings. The benefits are substantial, customer visits tend to focus on the laboratory area and as result of their exceptional standards they are always ‘tour ready’.
Andon & Visual Controls
2016 saw the introduction of electronic performance boards in each area of production. These allow operators and managers to see at a glance how each line is performing against Takt (pace of customer demand).
One of the most popular ideas pinched with pride by visitors is the Fujifilm Ideas programme – IPICS. This stands for Idea, Plan, Implement, Check Sustain.
This is managed through a simple t-card system developed in-house. Ownership of each idea is the initiator and activities are monitored by the team leaders. A monthly reward and recognition programme support this. To re-enforce the effectiveness of this programme in the last four years Fujifilm have seen the following results
- 3039 Ideas submitted
- 753 Declined
- 2286 Implemented
Communication, Communication, Communication
Fujifilm truly believe that the bedrock of any successful lean programme is communication. If employees don’t know what is happening, they can’t possibly support or replicate it. Excellent communication allows you to gain, and sustain, momentum. When drawing up a lean programme it is imperative you address how activities and actions are disseminated. Fujifilm share their communication programme which includes:
- Lean Awareness Training
- Five senior management briefings per year
- Employee communication forum
- Operator Issue Boards
- Strategy (Plan), vision & Values posted
- Comments boxes – answered every month!
- Annual employee survey
- Television communications channel
- Daily stand-up meetings & 5 min cell briefings
This seems a lot, but it all works on a holistic level, ensuring everyone who works at the site has clarity on where and what is happening. Most importantly Gary Burgess, CI Manager at the site truly believes that a Daily Gemba (walking the line) is the key to sustaining lean at such a high level.
Our thanks go to Gary Burgess, Gary Page and Adam Murrell and all of the team at Fujifilm who gave up their time to share best practice with others.